
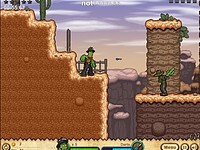
Yes when we are going that thick we are doing rings. Are you welding it together on the seam? Is your roller handling the 3/8" thickness okay? a 48" roll set sounds sort of light for that thickness for any kind of length. I might not even turn the piece to roll it again, depending on how true the roll is in one direction. Higher yield steels are uncooperative at best! With 3/8" at that diameter low carbon steel I think I would do the same as what you are doing. Remember the inside surface is being compressed and the outside surface is being stretched, so your material type plays a big role in the success of a given calculation. The thicker the material, the more difficult it is to get the exact size.

I don't have any of my old fab notes here, but I used to have a formula for everything every type of material, thickness, and forming method. For example, I used to calculate sheet metal (under 1/8") using a completely different formula and never taking the NA into consideration (the number is just too small to make a difference, especially for plain old sheet steels). Material thickness counts for a lot, though. There are probably as many different methods for calculating BA as I have fingers and toes! I always use the neutral axis (theoretical centerline of the material thickness), because that's how I learned.
